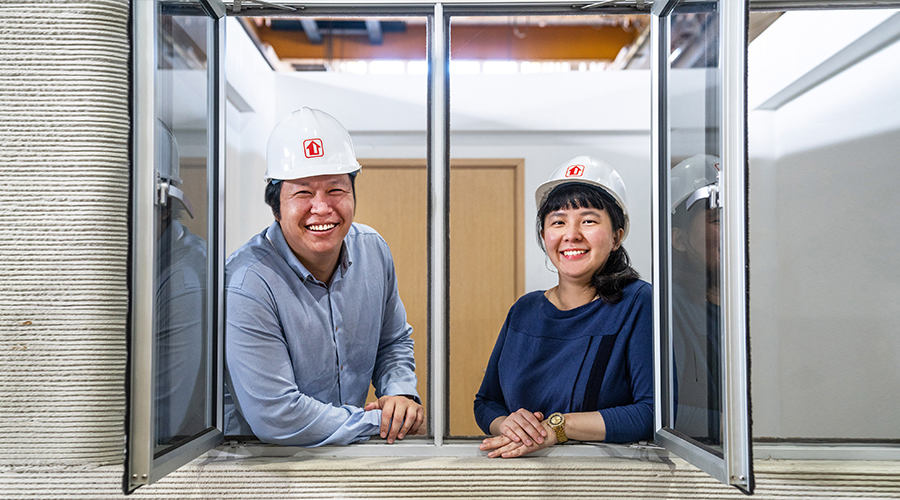
At first glance, with its concrete walls and floor, the room looked like any other newly-constructed room of a Build-To-Order (BTO) flat. It is, however, no ordinary room, as it was printed by the largest 3D concrete printer in South-east Asia, at HDB's Centre of Building Research (CBR).
A Game Changer
The foray into 3D printing is part of HDB's ongoing efforts to embrace game-changing construction innovations, such as Prefabricated Bathroom Units and Prefabricated Prefinished Volumetric Construction (PPVC), in its continual quest to enhance construction productivity and build better quality homes.
Construction using 3D concrete printing combines digital Building Information Modelling (BIM) technology with additive manufacturing techniques, a process in which objects are constructed by adding layers of materials. Leading HDB's 3D concrete printing initiative is a team from HDB's Building and Research Institute, which includes engineers Lim Emiko and Chew Jia Han.
“3D concrete printing lets us create objects with intricate details or geometric forms that would be near impossible with conventional precast construction methods,” explains Emiko. “The entire process is highly automated, and could help us achieve even greater construction productivity.”
Unlocking the Potential of 3D Concrete Printing
The technology, however, is still emerging in terms of its application in concrete building construction. “When it comes to 3D concrete printing, we are dealing with many unknowns,” Jia Han shares. “A lot of factors and parameters can affect the entire printing session. For instance, the printer nozzle can get clogged, and we would need to configure the machine before printing can continue.”
Unfazed by the challenges, the team persevered and its efforts eventually paid off—after many printing trials, HDB's first 3D printed room was successfully completed in just 13 hours. Including the insertion of reinforcement bars, the process took about 6 days. “All of us breathed a huge sigh of relief when the printing was completed,” Jia Han says. “It's something that has never been done before, and we are proud to be part of this pioneer team.”
The free-form production of concrete elements opens up a whole new world of possibilities. For a start, HDB will trial the use of 3D concrete printing for precinct design features at selected Build-To-Order projects in Tengah and Bidadari.
“Free-form and bespoke designs in landscape furniture and architectural features can offer greater variety in the look, feel, and texture of the housing developments,” Emiko explains.
Homes of the Future
Building on these efforts, HDB's research will expand to other areas to enhance the printer's capabilities, such as using multiple nozzles to increase printing productivity, and developing a robotic system to place steel reinforcements into the concrete during the printing process for structurally sound construction. To help HDB best leverage the potential of this advanced technology, the team constantly keeps itself up-to-date with the latest research, and learning from experts worldwide.
“This technology can potentially change the way we build homes, and this successful trial serves as a prelude to more exciting things to come,” Jia Han smiles. “At the end of the day, our goal is always to build safer, smarter, and better homes for Singaporeans.”